Blog
What is Co-Extrusion WPC Decking?
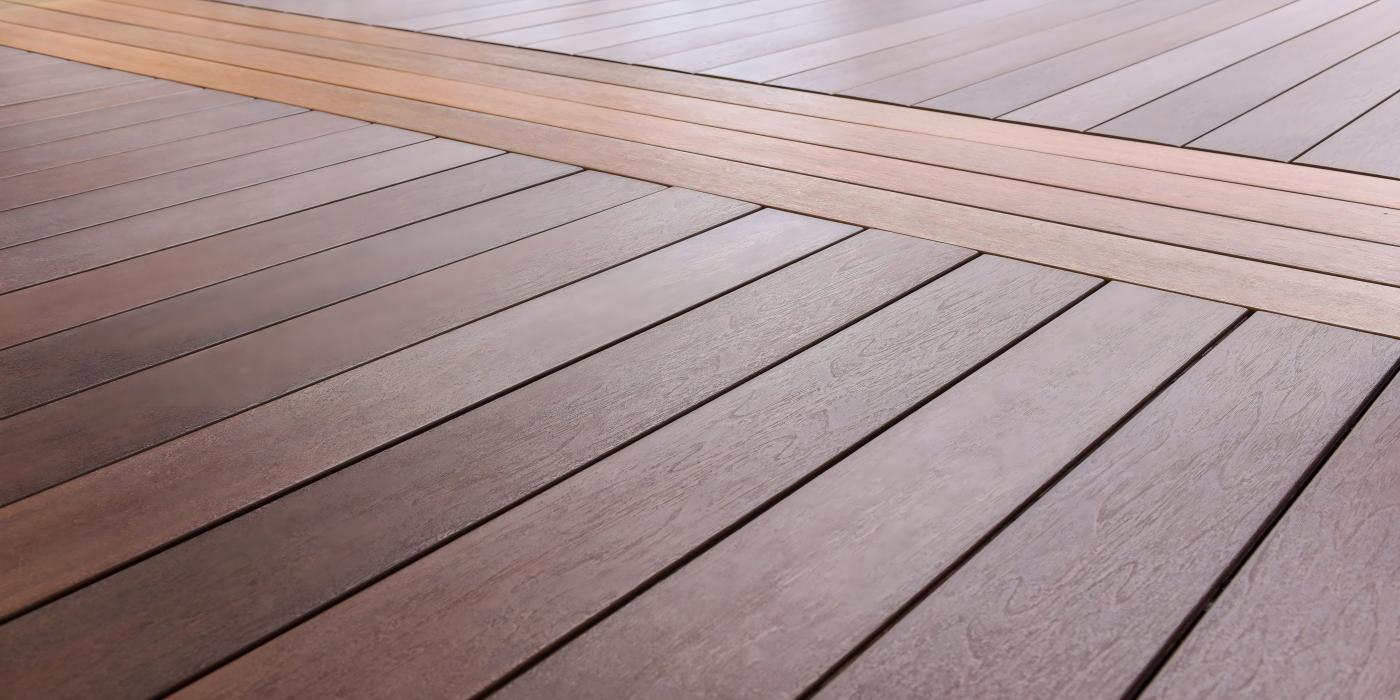
Co-extrusion WPC Decking: A Technical Deep Dive into Advanced Composite Building Materials
Co-extrusion WPC (Wood-Plastic Composite) decking represents a significant evolution in engineered outdoor building materials. Combining layered manufacturing precision with advanced polymer science, this technology addresses longstanding limitations of traditional decking solutions. Below, we explore its structural composition, manufacturing process, performance advantages, and industry applications.
Table of Contents
Toggle1. Defining Co-Extrusion WPC Decking
Co-extrusion WPC decking is a multi-layered composite material engineered through simultaneous extrusion of distinct polymer-wood formulations. Unlike monolithic WPC (a uniform blend of wood fibers and plastics), co-extrusion technology creates:
-
- Protective Cap Layer: A 0.6–1.5mm polymer-rich shell (typically HDPE or PVC) with UV inhibitors, anti-slip additives, and color stabilizers.
-
- Structural Core: A wood-plastic composite substrate (60–70% hardwood fibers, 30–40% recycled polymers) optimized for load-bearing capacity.
-
- Ventilation/Drainage Layer: Engineered grooves (2–3mm depth) on the board’s underside to mitigate moisture retention.
This stratified design enables targeted performance enhancements while maintaining a 95% recycled material composition.
2. The Manufacturing Process: Precision Engineering
The production of co-extrusion WPC decking involves three critical phases:
Phase 1: Material Preparation
-
- Wood Fiber Treatment: Hardwood flour is dried to ≤0.8% moisture content and filtered to 80–120 mesh size.
-
- Polymer Compounding: Recycled HDPE/PP is blended with coupling agents (maleic anhydride) and stabilizers (HALS) in a 2:1 ratio.
Phase 2: Co-Extrusion
-
- Dual extruders operate at 230–270°C, maintaining separate material streams for cap and core layers.
-
- Bonding occurs under 10–15MPa pressure, ensuring molecular adhesion without adhesives.
-
- Cooling profiles are controlled at 0.5–1.0°C/sec to prevent warping and internal stresses.
Phase 3: Surface Finishing
-
- Embossing: 150–200PSI hydraulic presses replicate natural wood grain textures (Janka hardness ≥800).
-
- UV Curing: Optional nano-ceramic coatings (5–8μm) enhance scratch resistance (Taber Abrasion ≥3,000 cycles).
3. Performance Advantages Over Traditional Decking
Independent testing data highlights co-extrusion WPC’s superiority:
Moisture Resistance
-
- Water Absorption: 0.4–0.9% after 30-day immersion (ASTM D570) vs. 5–15% for standard WPC.
-
- Swelling Resistance: ≤0.12% volumetric expansion in 90% humidity (EN 317).
Thermal Stability
-
- Linear Expansion: 0.06–0.09% per 10°C temperature change (ASTM D1041) — 50% lower than monolithic WPC.
-
- Heat Deflection Temperature: 85–95°C (ASTM D648), suitable for desert climates.
Structural Integrity
-
- Flexural Strength: 35–45MPa (EN 310) — comparable to tropical hardwoods like Ipe.
-
- Impact Resistance: 15–20 kJ/m² (ISO 179) — withstands heavy foot traffic and falling objects.
Aesthetic Longevity
-
- UV Fade Resistance: ΔE ≤2.5 after 3,000 hours of xenon-arc exposure (ISO 4892).
-
- Mold Resistance: 0% fungal growth after 28 days in ASTM G21 testing.
4. Industry Applications & Cost-Benefit Analysis
Residential Use
-
- Pool Decks: Chlorine and saltwater resistance (ASTM D543 testing).
-
- Rooftop Terraces: 30% lighter than concrete pavers (1.1–1.3g/cm³ density).
Commercial Projects
-
- Boardwalks: Meets ADA slip-resistance standards (≥0.6 wet SCOF).
-
- Restaurant Patios: Fire Rating Class B (ASTM E84; Flame Spread ≤50).
Lifecycle Cost Comparison
Metric | Co-Extrusion WPC | Pressure-Treated Wood | PVC Decking |
---|---|---|---|
Initial Cost ($/sq.ft) | 8.50–12.00 | 4.00–6.50 | 10.00–14.00 |
25-Year Maintenance | $0.30 | $4.80 | $1.20 |
Residual Value (%) | 65–70 | 10–15 | 40–50 |
Data source: National Association of Home Builders (2023 Material Lifecycle Report)
5. Installation Best Practices
To maximize co-extrusion WPC’s performance:
-
- Joist Spacing: 16″ on-center (356mm) for 20mm boards; 12″ (305mm) for 25mm+ profiles.
-
- Gapping: 3–5mm between boards (accounts for thermal movement).
-
- Fasteners: Stainless steel clips (Grade 316) prevent thermal bridging.
6. Environmental Compliance for Co-Extrusiong WPC Decking
-
- Recycled Content: ≥85% by weight (ISO 14021 certified).
-
- Low VOC Emissions: ≤50μg/m³ (CDPH Standard Method v1.2).
-
- End-of-Life Recycling: Fully grindable for reuse in new WPC production.
Conclusion: The Future of Outdoor Surfaces
Co-extrusion WPC decking combines material science innovation with sustainable manufacturing, delivering a 30+ year service life under extreme conditions. As architects and builders increasingly prioritize durability and lifecycle costs, this technology is redefining expectations for outdoor surfaces — proving that high-performance materials need not compromise aesthetics or environmental responsibility.
-
- Want a sample for our Co-extrusion WPC decking? Please Contact Us Or check our Co-extrusion WPC Decking Products