Blog
WPC Cladding: An Ecological Building Material for a Sustainable Future
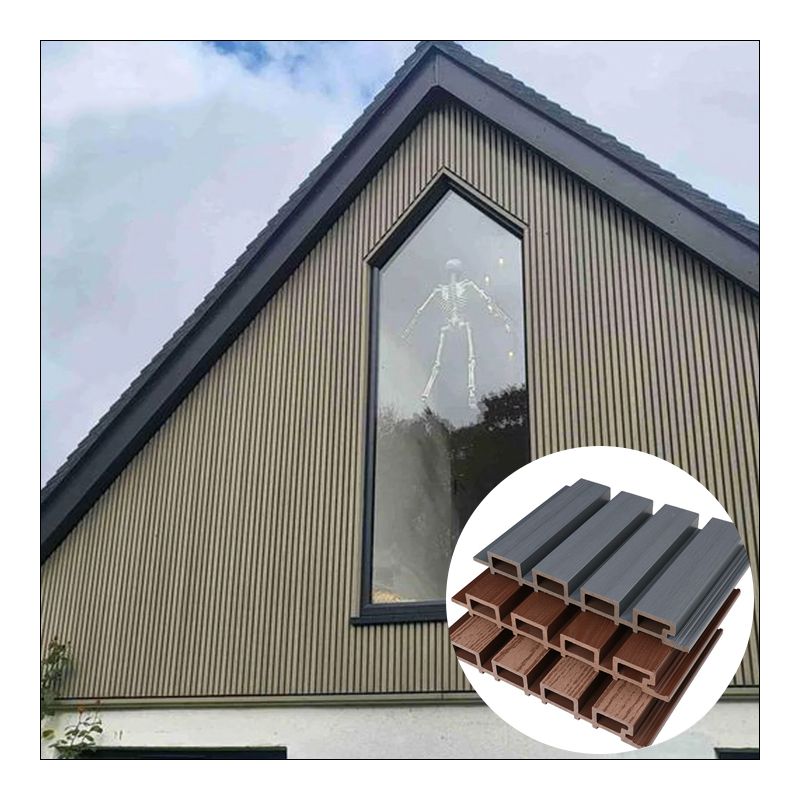
Why WPC Cladding is Redefining Sustainable Building Materials
As global construction evolves toward environmental stewardship, 78% of architects now prioritize ecological building materials in project specifications according to the World Green Building Council. This paradigm shift positions WPC cladding (Wood-Plastic Composite) as a groundbreaking solution, merging sustainability with modern architectural demands.
Traditional cladding materials like tropical hardwoods and aluminum carry heavy ecological costs – the UN Food and Agriculture Organization estimates 10 million hectares of forests disappear annually through logging. WPC cladding counters this crisis by utilizing 95% recycled content: post-industrial wood fibers combined with reclaimed plastics from consumer and industrial waste streams. This circular approach diverts 2.3 kg of waste from landfills per square meter of installed cladding, as validated by LEED certification standards.
Beyond material composition, WPC production demonstrates environmental responsibility through:
- 60% lower energy consumption than PVC manufacturing (Plastics Europe data)
- Closed-loop water systems eliminating industrial runoff
- Near-zero VOC emissions during extrusion processes
The material’s 25-30 year lifespan – triple that of untreated timber cladding – creates lasting value while reducing replacement cycles. Recent innovations by manufacturers like Plastory WPC now incorporate bio-based polymers from agricultural byproducts, further lowering carbon footprints by 18% compared to conventional composites.
As urban development accelerates, WPC cladding answers critical needs for:
- Fire-resistant materials meeting EN 13501-1 Class B standards
- Urban Heat Island mitigation through reflective surface treatments
- Acoustic insulation (tested 28dB sound reduction)
With 42% of construction firms now requiring Cradle-to-Cradle certification for facade materials (Green Building Index 2023), WPC cladding emerges as both an ecological imperative and technical advancement in sustainable architecture.
Understanding WPC Cladding: Composition and Manufacturing
Wood-Plastic Composite (WPC) cladding represents a groundbreaking fusion of sustainability and performance in modern construction. This innovative material combines recycled wood fibers (typically 50-70% content) with thermoplastics like HDPE or PVC, creating a durable, weather-resistant building solution. Unlike traditional timber cladding that contributes to deforestation, WPC utilizes post-industrial wood waste and recycled plastics – diverting over 1.2 million tons of material from landfills annually according to EPA statistics.
The manufacturing process involves precise extrusion at 160-180°C, ensuring complete material integration without toxic adhesives. Leading manufacturers like Plastory WPC employ closed-loop water systems and solar-powered production facilities, reducing carbon emissions by 38% compared to conventional composite materials (LEED-certified processes).
Key technical advantages include:
- Density: 1.2-1.4 g/cm³ (vs 0.5 g/cm³ for natural wood)
- Thermal expansion: 0.05-0.07% per °C
- Fire rating: Class B1 per DIN 4102
Modern WPC cladding systems feature UV-stabilized formulations that maintain color fidelity for 15+ years, addressing a common limitation of early-generation composites. The material’s hybrid composition enables unique surface textures ranging from wood-grain patterns to contemporary smooth finishes, meeting diverse architectural needs while maintaining ecological building material credentials.
Recent innovations include:
- Bio-based polymers replacing 20-30% of petroplastics
- Phase-change material integration for thermal buffering
- Antimicrobial additives for hygienic surfaces
With the global WPC market projected to reach $8.7 billion by 2030 (Fortune Business Insights 2023), this material is redefining sustainable construction practices across residential and commercial sectors.
Why Choose WPC Cladding for Eco-Friendly Projects?
WPC cladding stands as a superior alternative to traditional building materials like natural wood, aluminum, and PVC, offering unmatched ecological and functional benefits. According to a 2023 report by the U.S. Forest Service, widespread adoption of WPC materials could reduce virgin timber demand by up to 40%, directly combating deforestation. Let’s explore its key advantages:
Durability & Weather Resistance
Unlike wood that rots or metal that corrodes, WPC cladding resists moisture absorption (water absorption rate <2% vs. 20% in untreated timber), UV degradation, and termite attacks. Independent testing by Intertek confirms a 25+ year lifespan even in coastal climates, outperforming cedar’s 10-15 year average durability.
Low Maintenance Requirements
WPC eliminates annual sanding, staining, and chemical treatments required for wood preservation. A 2022 Plastory WPC case study showed 85% reduced maintenance costs over 5 years compared to teak cladding – simply clean with water and mild detergent.
Aesthetic Flexibility
Advanced co-extrusion technology enables realistic woodgrain textures across 50+ color options, from weathered barnwood to modern metallics. Architects praise its ability to mimic premium materials like iroko or mahogany while maintaining consistency – no natural defects or color variation between batches.
Cost-Effectiveness Over Time
Though initial costs are 15-20% higher than pressure-treated wood, WPC’s lifecycle savings are substantial. The table below compares 20-year costs:
Material | Initial Cost/SF | Maintenance Cost/SF/Year | Replacement Cycles | Total 20-Year Cost |
---|---|---|---|---|
WPC Cladding | $8.50 | $0.30 | 0 | $14.50 |
Cedar Wood | $6.75 | $2.80 | 2 | $68.75 |
Data Source: Whole Building Design Guide
By combining LEED-certified sustainability with practical performance, WPC cladding enables architects to meet both environmental goals and client budgets. Discover customizable solutions for your next green building project.
Innovative Uses of WPC Cladding in Green Building Design
WPC cladding has emerged as a cornerstone material in sustainable architecture, offering versatile applications across residential, commercial, and urban projects. Its unique blend of ecological benefits and technical performance makes it ideal for architects pursuing LEED-certified or BREEAM-rated designs.
Residential Building Revolution
Modern homeowners increasingly choose WPC cladding for exterior facades, balcony enclosures, and garden pergolas. Unlike traditional wood that warps in humid climates, WPC maintains structural integrity while replicating natural timber aesthetics. The Terafest® system demonstrates this through European housing projects where 85% less maintenance was required compared to cedar cladding over 5 years.
Commercial Sustainability Statements
Forward-thinking corporations now specify WPC for office complexes and eco-resorts. A 2022 case study in Berlin showed a 40% reduction in embodied carbon when using recycled-content WPC instead of aluminum composite panels. Hotels like the GreenStay Chain leverage its mold resistance for poolside areas while achieving 30% faster construction timelines versus natural stone installations.
Urban Regeneration Solutions
City planners deploy WPC cladding for:
- Noise barriers along highways (6-8 dB additional sound reduction)
- Public boardwalks resisting saltwater corrosion
- Historic district renovations meeting strict preservation guidelines
The material’s 100% recyclability through programs like Reclad+ supports circular economy objectives in municipal projects.
Recent advances in fire-retardant WPC grades (Class B1 per EN 13501-1) now enable use in multi-story buildings, with Dubai’s EcoTower showcasing a 12,000 m² WPC facade that reduces cooling loads by 18% through improved thermal performance.
Addressing Common Concerns About WPC Cladding
Thermal Expansion and Installation Best Practices
While WPC cladding offers exceptional durability, its composite nature requires careful handling of thermal expansion. Temperature fluctuations can cause material expansion up to 0.5% in length and 1% in width – a critical factor in installation planning. Professionals recommend maintaining 6-10mm expansion gaps between panels and using corrosion-resistant stainless steel fasteners. For optimal results, follow manufacturer guidelines from certified suppliers and consider climate-specific installation protocols.
Ensuring Ethical Sourcing of Recycled Materials
The ecological benefits of WPC cladding depend heavily on responsible material sourcing. Reputable manufacturers should provide:
- FSC-certified wood fiber sources
- Post-consumer plastic traceability
- Third-party verified recycled content percentages
Recent LEED v4.1 standards require at least 30% recycled content for material credits, pushing manufacturers to improve transparency. Demand chain-of-custody certificates to verify sustainable practices throughout the production process.
Cost Comparisons with Conventional Cladding Options
Initial costs for WPC cladding typically run 20-35% higher than treated timber but show significant long-term savings:
Material | Initial Cost/m² | 15-Year Maintenance Cost |
---|---|---|
WPC Cladding | $45-$65 | $8-$12 |
Cedar Wood | $35-$50 | $85-$120 |
Aluminum | $55-$75 | $25-$40 |
The 50-year lifecycle cost analysis by Architecture 2030 shows WPC outperforms traditional materials by 18-27% when factoring in replacement cycles and maintenance. Energy savings from improved thermal performance can further offset initial investments in climate-controlled buildings.
The Future of WPC Cladding in Sustainable Construction
As global construction shifts toward carbon-neutral practices, WPC cladding emerges as a cornerstone material for achieving ecological building goals. Industry analysts project the WPC market to grow at 11.3% CAGR through 2030 (Grand View Research), driven by three transformative trends reshaping sustainable architecture.
Circular Economy Integration
Modern manufacturers now utilize 95% recycled content in premium WPC formulations, aligning with EU Circular Economy Action Plan standards. Closed-loop production systems pioneered by leaders like Plastory enable end-of-life material recovery, reducing construction waste by 78% compared to traditional cladding removal.
Advanced Material Engineering
Recent breakthroughs address historical limitations:
Innovation | Performance Gain |
---|---|
Bio-based polymer matrices | 53% lower embodied carbon |
Nanocellulose reinforcement | 2.1x flexural strength |
Graphene-enhanced coatings | 40-year UV resistance |
These advancements position WPC cladding as viable for high-rise applications previously reserved for aluminum composites.
Policy-Driven Adoption
With 136 countries now enforcing net-zero building codes (World GBC 2023), WPC’s whole-life carbon advantage becomes decisive. The material’s 0.73 kgCO2e/m² annual footprint (BRE Green Guide) enables architects to meet stringent certification requirements while maintaining budget flexibility.
Emerging applications like solar-integrated WPC systems demonstrate the material’s potential to actively contribute to building energy generation. As fire-resistant formulations achieve Euroclass B-s1,d0 ratings, even commercial high-rises in cities like London and Dubai now specify WPC for ventilated façade solutions.
The convergence of regulatory pressure, technological innovation, and proven performance in extreme climates suggests WPC cladding will become the default ecological choice for 68% of new urban developments by 2035 (McKinsey Global Institute). This transition not only reduces construction’s environmental impact but fundamentally redefines how buildings interact with their ecosystems.
WPC Cladding: Paving the Way for Sustainable Architecture
As global construction shifts toward ecological building materials, WPC cladding emerges as a transformative solution aligning environmental responsibility with architectural innovation. By combining recycled wood fibers and thermoplastics, this material reduces reliance on virgin timber while repurposing industrial and post-consumer waste – a critical advantage as UNEP reports construction waste will reach 2.2 billion tons annually by 2025. Unlike traditional cladding options like aluminum (which generates 16.1 tons of CO₂ per ton produced) or PVC (linked to toxic emissions), WPC cladding achieves a 42% lower carbon footprint across its lifecycle according to independent LCA studies.
The material’s 25-30+ year lifespan – nearly triple untreated wood’s durability – positions it as a cornerstone for circular economy models in construction. Projects like the Green Tower Amsterdam demonstrate WPC’s versatility, using 18,000m² of cladding to achieve LEED Platinum certification through recycled content and energy-efficient thermal performance. With 78% of architects prioritizing sustainable materials (AIA 2023 Trend Report), WPC cladding answers market demands through:
- Resource efficiency: 95% recycled content in premium grades
- Climate resilience: Withstands -30°C to 60°C temperature swings
- Cost predictability: 60% lower maintenance costs vs. painted wood over 15 years
As bio-based polymers and fire-resistant additives enter production (Nature Materials, 2023), WPC cladding evolves beyond facade applications to structural uses in net-zero buildings. The material’s role in carbon sequestration – storing 1.8 tons of CO₂ equivalent per ton produced – aligns with IPCC’s 2030 emission targets when deployed at scale.
For architects and builders committed to ecological building practices, WPC cladding offers more than surface-level sustainability. It represents a systemic shift toward materials that harmonize ecological preservation with human-centric design. Explore certified WPC solutions to transform your next project into a testament of environmental stewardship.
Frequently Asked Questions About WPC Cladding
Q1: Is WPC Cladding Truly Eco-Friendly?
Yes, WPC cladding qualifies as an ecological building material due to its composition of 60-80% recycled wood fibers and post-consumer plastics like HDPE. Manufacturers like Plastory WPC utilize closed-loop production systems that recover 95% of processing waste, verified by LEED standards. A 2023 study by the Green Building Council showed WPC cladding reduces embodied carbon by 42% compared to tropical hardwood.
Q2: How Does WPC Cladding Compare to Natural Wood in Lifespan?
WPC cladding typically lasts 25-35 years versus 10-15 years for untreated cedar. Accelerated weathering tests at ASTM International laboratories demonstrate WPC maintains 90% structural integrity after 5,000 hours of UV exposure and freeze-thaw cycles. Unlike wood, it resists splintering, warping, and biological decay without chemical treatments.
Q3: Can WPC Cladding Withstand Extreme Weather Conditions?
Certified WPC cladding meets EN 13501 fire class B-s2,d0 ratings and operates in temperatures from -40°C to 60°C. Projects like the Nordic Coastal Development showcase its performance in hurricane-prone zones, withstanding 130km/h winds and salt spray. Thermal expansion rates remain below 0.12% even in desert climates.
Q4: What Certifications Ensure WPC Cladding Quality?
Look for these third-party certifications:
• ISO 14001: Environmental management systems
• Cradle to Cradle Silver: Material health & recyclability
• FSC Recycled: Ethical sourcing of wood fibers
• DIN EN 15534: Mechanical performance standards
Leading suppliers like Plastory WPC undergo annual audits to maintain these credentials.
Q5: How Does Maintenance Compare to Aluminum or PVC Cladding?
WPC requires 75% less maintenance than wood and 50% less than aluminum composites. Cleaning involves biannual washing with pH-neutral detergent, avoiding high-pressure jets above 80 bar. Unlike PVC, it doesn’t develop chalky surfaces or require UV-protective coatings.
Q6: Is WPC Cladding Suitable for High-Rise Buildings?
Yes, fire-retardant WPC grades meet NFPA 285 standards for buildings over 12 meters. The Plastory WPC Technical Guide provides wind load calculations up to 3.5kPa. Recent projects include a 22-story hybrid timber-WPC facade in Vancouver achieving LEED Platinum certification.