Blog
The Environmental Friendliness of Wood-Plastic Composite (WPC) Decking
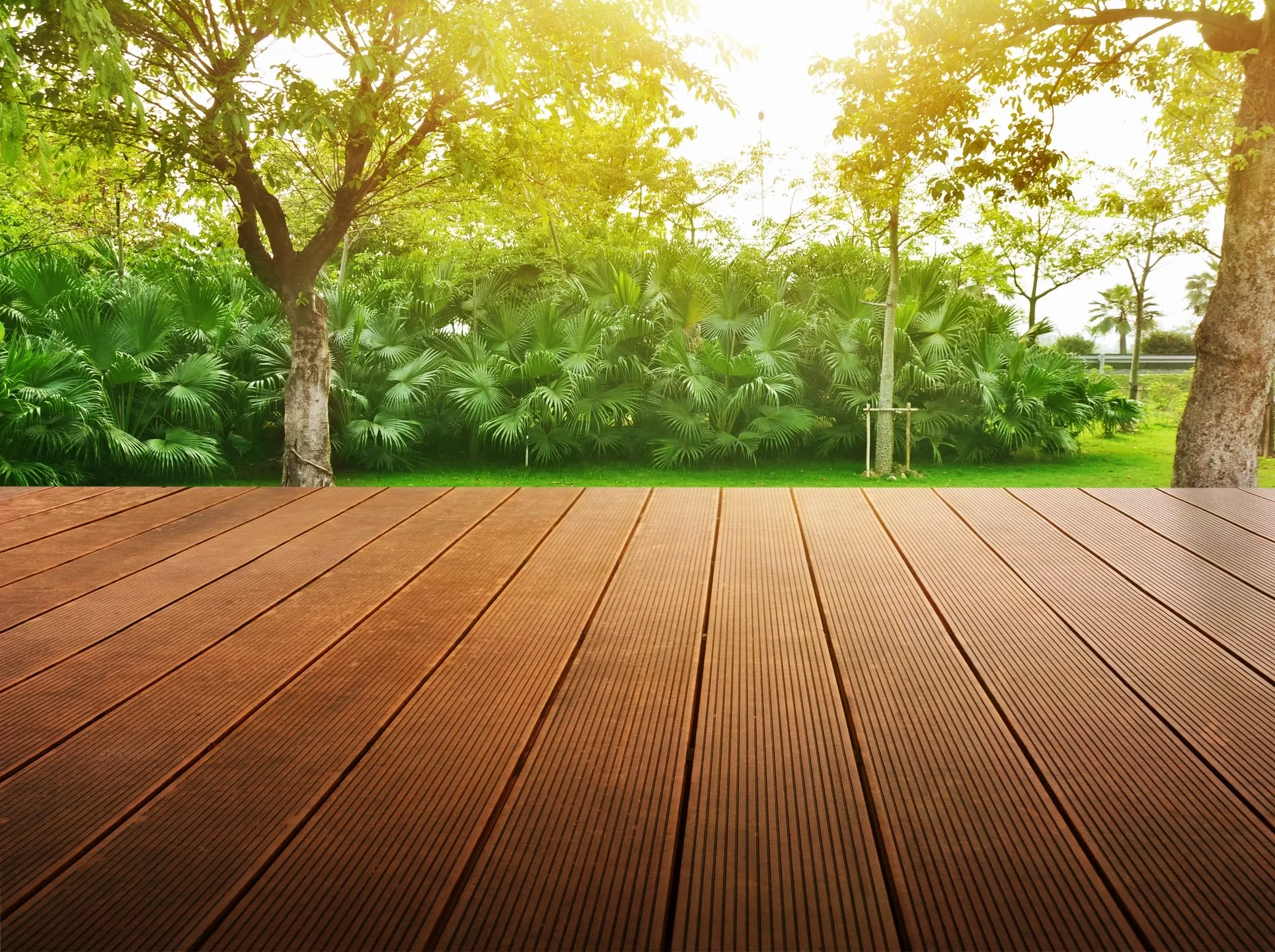
1. Introduction
Wood-plastic composite (WPC) decking has gained considerable traction in recent years as a potential alternative to traditional wood decking. This increasing popularity stems from growing awareness of environmental issues and demand for more sustainable building materials. This report provides a comprehensive analysis of the environmental friendliness of WPC decking by examining its material composition, manufacturing processes, lifecycle considerations, and by comparing its environmental impact with that of traditional wood decking. A thorough evaluation of the environmental claims associated with WPC decking is crucial for enabling informed decision-making within the construction industry, among academic researchers, and for environmentally conscious consumers seeking sustainable outdoor building solutions.
2. What is Wood-Plastic Composite (WPC) Decking?
2.1 Definition and Material Composition
Wood-plastic composite (WPC) decking is a composite material engineered from a combination of wood fibers (in the form of wood flour or wood pulp) and thermoplastic polymers [1]. The typical ratio of wood to plastic in WPC decking generally falls within the range of 50 to 70 percent wood content and 30 to 50 percent plastic content, though these proportions vary depending on the manufacturer and intended application [2]. For instance, some manufacturers produce WPC with compositions around 60% wood fibers and 35% plastic polymers [3], while others opt for a higher wood content of approximately 70% combined with 30% recycled plastic [4]. This higher proportion of wood content in many WPC formulations suggests a greater reliance on renewable resources compared to decking options made entirely of plastic.
The wood components utilized in WPC production are diverse, often including byproducts from various industries, such as sawdust, pulp, bamboo, peanut hulls, and other wood waste generated from woodworking operations or agricultural processes [5]. The ability to incorporate these diverse and often waste-derived wood sources positions WPC as a potential avenue for reducing waste streams from multiple sectors, contributing to a more circular approach to resource utilization.
Commonly employed thermoplastic polymers in WPC manufacturing include high-density polyethylene (HDPE), low-density polyethylene (LDPE), polyvinyl chloride (PVC), polypropylene (PP), and polylactic acid (PLA) [6]. The selection of polymer significantly influences the overall environmental footprint of the WPC material. For example, HDPE, frequently recycled from post-consumer sources like milk jugs and detergent bottles, is often considered more environmentally benign than PVC in many applications.
Case Study: Trex Decking’s Material Composition
Trex, a leading manufacturer of WPC decking in North America, exemplifies the industry’s approach to material composition. Their standard decking products contain approximately 95% recycled materials – a combination of reclaimed wood fiber and recycled plastic film from grocery bags, sandwich bags, and shrink wrap [7]. Each year, Trex repurposes over 400 million pounds of plastic waste and reclaimed wood, demonstrating the substantial waste diversion potential of WPC production at scale.
In addition to primary components, WPC formulations typically include various additives that enhance the material’s properties and appearance [8]. These additives include:
- Coupling agents, such as maleic anhydride-grafted polypropylene (MAPP), which improve the bonding between wood fibers and plastic matrix
- Stabilizers to protect against UV exposure and thermal stress
- Foaming agents to reduce density
- Dyes and pigments for color
- Lubricants to improve surface finish and processing characteristics
- Fungicides to enhance resistance to fungal growth [9]
While these additives are crucial for performance and aesthetics, their environmental impact—including sourcing and potential toxicity—warrants consideration in a comprehensive environmental assessment. Some additives might derive from non-renewable resources or possess the potential to leach into the environment over extended periods.
2.2 Manufacturing Processes of WPC Decking
The manufacturing of WPC decking generally involves a two-step process [10]. First is compounding. In this process, wood particles like flour, fibers, or pulp are mixed with thermoplastic polymer and additives. This creates a smooth, dough-like mixture. This mixing can be conducted in batches or through a continuous process [11]. The second step involves forming the composite material into the desired shape of decking boards or other products [12].
Three primary methods are employed for forming WPC:
- Extrusion: This is the most common method. In this process, molten composite material is pushed through a die. The die is a shaped opening that decides the final shape of the decking board [13]. Extrusion’s prevalence suggests it is likely the most energy-efficient method for producing consistent profiles at scale, as continuous processes often exhibit lower energy consumption per unit compared to batch processes.
- Injection molding: Involves injecting molten composite under high pressure into a cold mold cavity, where it solidifies into the desired shape [14].
- Compression molding: The molten composite is placed between two halves of a mold and compressed under heat and pressure to take the shape of the mold cavity [15].
Some manufacturers employ co-extrusion, where a tough polymer shell is applied to the composite core, providing enhanced protection against weathering, scratches, and stains [16]. While co-extrusion improves durability, the environmental impact of the additional polymer layer and manufacturing step needs consideration in the overall assessment, as it introduces another material component and processing stage, potentially increasing the embodied energy of the final product.
Case Study: TimberTech’s Manufacturing Innovation
TimberTech, another major WPC manufacturer, has implemented closed-loop water cooling systems in their manufacturing facilities, reducing water consumption by up to 96% compared to traditional manufacturing methods. Additionally, they’ve invested in energy-efficient extrusion technology that reduces energy consumption by approximately 15% compared to industry standard equipment [17]. This case highlights how innovations in manufacturing processes can significantly mitigate some of the environmental considerations associated with WPC production.
2.3 Comparison of WPC with Traditional Wood and Other Decking Materials
WPC decking exhibits several key differences when compared to traditional solid wood decking [18]. Traditional wood decking is sourced directly from harvested trees, potentially involving unsustainable logging practices, whereas WPC utilizes recycled plastics and wood waste, reducing demand for virgin timber. Traditional wood requires regular maintenance, including staining, sealing, and treatment with chemical preservatives to protect against rot, decay, and insect infestation. In contrast, WPC is inherently more resistant to these issues due to its plastic content, resulting in significantly lower maintenance requirements. Traditional wood’s durability varies depending on species and maintenance effectiveness, while WPC generally offers consistent durability, resistant to weathering, UV light, and pests. These differences have significant implications for the overall environmental impact across the lifecycle of both materials.
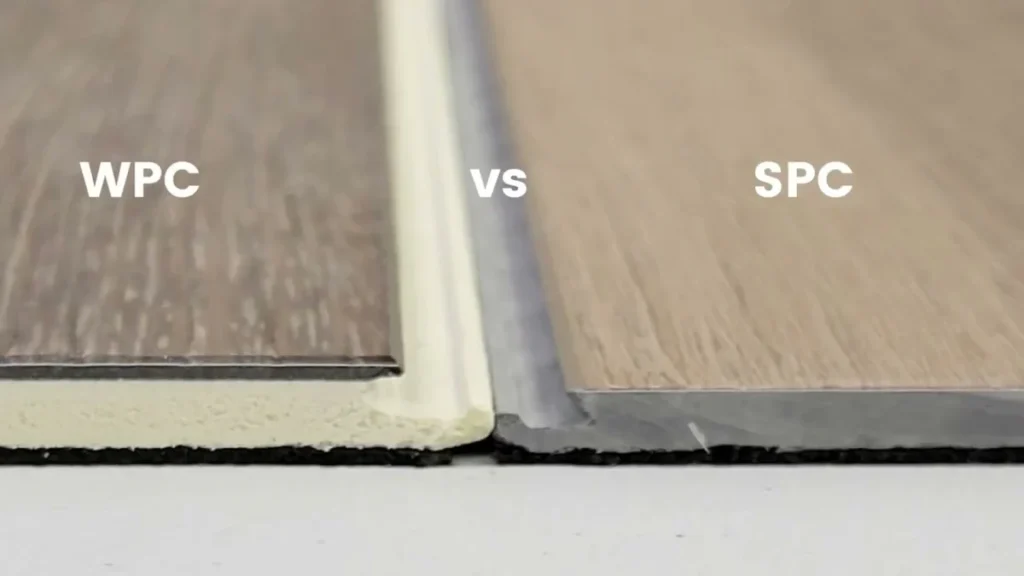
When comparing WPC to other alternative decking materials, such as PVC decking, further distinctions emerge [19]:
Feature | WPC Decking | PVC Decking | Traditional Wood |
---|---|---|---|
Composition | Wood fibers + plastic | Pure synthetic PVC resin | Natural wood |
Appearance | More natural, wood-like | Uniform, slightly plastic feel | Natural wood grain |
Maintenance | Low (occasional cleaning) | Lowest (simple cleaning) | High (regular treatment) |
Environmental Impact | Moderate (uses recycled materials) | Higher (unless using recycled PVC) | Variable (depends on sourcing) |
Cost | Mid-range | Highest | Lowest (initially) |
Lifespan | 25-30 years | 30+ years | 10-30 years (species dependent) |
This comparison reveals potential trade-offs between recycled content use (a key environmental advantage of WPC), durability, and maintenance requirements. The selection of the “most environmentally friendly” decking material depends on specific priorities and application context. An environmentally conscious consumer might prioritize recycled materials, while another might emphasize longevity and minimal maintenance, leading to different material choices.
3. Environmental Advantages of WPC Decking
3.1 Utilization of Recycled Materials
A significant environmental advantage of WPC decking lies in its ability to utilize recycled materials [20]. WPC production commonly incorporates recycled plastics, such as high-density polyethylene (HDPE) from post-consumer waste like plastic bottles, and reclaimed wood in various forms, including sawdust and wood chips generated as waste from woodworking and manufacturing processes [21].
Typical WPC decking products contain substantial amounts of recycled content. For example, some manufacturers produce decking where the plastic component (approximately 30-40% of the material) is entirely recycled [22]. The incorporation of these recycled materials directly addresses the growing global issue of plastic and wood waste by diverting them from landfills, conserving landfill space, and reducing environmental pollution associated with waste disposal.
Case Study: AZEK’s Recycling Impact
AZEK Building Products, which manufactures TimberTech composite decking, reported in 2021 that they diverted approximately 500 million pounds of waste from landfills annually through their recycling program. The company collects post-industrial wood fiber that would otherwise be incinerated or landfilled, and incorporates post-consumer recycled plastic from sources including bottle caps, packaging film, and medical tubes [23]. This demonstrates the significant potential for waste diversion through WPC production.
Utilizing recycled materials generally has a lower energy footprint compared to virgin material production, contributing to reduced overall energy consumption and greenhouse gas emissions. This use of recycled materials contributes to a more circular economy model, where waste products are repurposed and given new life, reducing reliance on finite resources. The potential for WPC itself to be recycled at the end of its lifespan [24] further enhances this circularity, provided effective recycling infrastructure and processes exist.
3.2 Reduced Deforestation and Conservation of Natural Resources
WPC production helps conserve forests and natural resources by lessening demand for virgin timber [25]. By utilizing wood waste and recycled wood fibers as primary components, WPC offers a way to use wood resources more efficiently and reduce pressure on natural forests. This contrasts with traditional wood decking, which requires tree felling, potentially leading to deforestation, habitat loss, and biodiversity reduction.
Forests play a crucial role in carbon sequestration, absorbing carbon dioxide and helping regulate climate. By relying on wood byproducts, WPC contributes to the conservation of these vital ecosystems and helps mitigate negative environmental impacts associated with deforestation, including soil erosion and disruption of water cycles.
3.3 Lower Maintenance Requirements and Reduced Chemical Use
WPC decking exhibits inherent resistance to rot, decay, insect infestation, and moisture absorption due to its plastic content [26]. This durability significantly reduces the need for regular maintenance treatments typically required for traditional wood decks [27]. Traditional wood often needs periodic staining, sealing, and application of chemical preservatives for protection from elements and biological degradation.
These maintenance activities have environmental drawbacks, including the production and use of potentially harmful chemicals. Many wood preservatives contain volatile organic compounds (VOCs) and other substances toxic to the environment and human health. The reduced need for such chemical treatments with WPC translates to lower environmental impact by avoiding the production, transportation, and potential leaching of harmful substances. Furthermore, reduced maintenance frequency saves time and resources for end-users.
3.4 Durability and Extended Lifespan
WPC decking is known for its durability and potential for extended service life compared to traditional wood [28]. Its resistance to weathering, UV light, rot, decay, and insect damage contributes to longevity. While exact lifespan varies depending on product quality and environmental conditions, some sources suggest potential lifespans ranging from 10 to 100 years [29].
This increased longevity significantly reduces replacement frequency, leading to lower overall material consumption and waste generation over the long term. When decking lasts longer, fewer resources are needed for manufacturing new materials and disposing of old ones, lessening the environmental burden associated with both production and waste management.
Case Study: Residential Deck Replacement Comparison
A study of residential decking in the Pacific Northwest compared the lifecycle impact of traditional pressure-treated wood decking versus WPC decking. The analysis found that while the initial environmental impact of WPC production was higher, over a 25-year period, the wood decking would require replacement at least once, resulting in approximately 2.1 times more cumulative material usage than the more durable WPC option [30]. This illustrates how durability can significantly affect long-term environmental impact assessments.
3.5 Potential for Recycling WPC
WPC materials are theoretically recyclable, meaning they can potentially be re-melted and re-formed into new products at the end of their useful life [31]. This recyclability offers potential to further enhance WPC’s environmental sustainability by contributing to a circular economy where materials remain in use as long as possible.
However, the actual environmental benefit of WPC’s recyclability depends on development and widespread adoption of effective recycling programs and technologies specifically designed for WPC. Currently, infrastructure for large-scale WPC recycling may be limited in some regions. If WPC isn’t readily recyclable in practice, a significant portion might still end landfilled at life’s end, negating some sustainability advantages. Efforts to improve WPC recycling infrastructure and processes are therefore crucial for realizing its full environmental potential.
4. Potential Environmental Considerations and Counterarguments
4.1 Energy Consumption in Manufacturing
The manufacturing of WPC decking, involving processes such as heating, mixing, and extrusion, can be energy-intensive [32]. The energy required for these processes contributes to the overall environmental footprint of the material. The energy source is critical in determining environmental impact. If manufacturing energy comes primarily from fossil fuels, WPC production’s carbon footprint could be substantial. Conversely, renewable energy utilization would significantly lower environmental impact.
Therefore, while WPC offers benefits through recycled material use, its manufacturing process’s energy intensity is a potential environmental drawback requiring consideration. A comprehensive life cycle assessment would be necessary to accurately compare energy consumption of WPC and traditional wood decking, considering all stages from raw material extraction to end-of-life disposal.
4.2 Use of Virgin Plastics and Additives
While WPC production is lauded for recycled plastic use, virgin plastic inclusion is sometimes necessary for quality control and performance requirements [33]. Virgin plastic production involves fossil fuel extraction and processing, with significant environmental consequences including resource depletion and greenhouse gas emissions. Therefore, reliance on virgin plastics, even partial, reduces WPC’s overall environmental benefit compared to scenarios using entirely recycled content.
Additionally, as mentioned earlier, WPC formulations include various additives to enhance performance and aesthetics [34]. The environmental impact of these additives—including sourcing, manufacturing, and potential for leaching or environmental persistence—needs careful consideration. A thorough environmental assessment of WPC should encompass lifecycle impacts of all components, not just primary wood and plastic fractions.
4.3 End-of-Life Disposal Challenges
Currently, the most common end-of-life scenario for WPC decking is landfill disposal due to limited infrastructure for effective and economical recycling. WPC’s plastic component is known for slow degradation in landfills, contributing to long-term waste accumulation. Furthermore, depending on plastic types and additives used, there’s potential for harmful substance leaching into surrounding soil and groundwater over time.
The lack of widespread, efficient WPC recycling infrastructure presents a significant challenge to its overall environmental sustainability. While recycled material use in production is positive, benefits diminish if the material isn’t effectively recycled at life’s end and instead landfilled. Developing robust, economically viable WPC recycling solutions is crucial for closing the material loop and maximizing environmental advantages.
5. Comparative Environmental Impact Data
The following table provides a comparative overview of the environmental impact of WPC decking versus traditional wood decking based on analysis of provided information and general material property knowledge. Specific data can vary depending on exact composition, manufacturing processes, and regional factors.
Table 1: Comparative Environmental Impact of WPC Decking vs. Traditional Wood Decking
Environmental Indicator | WPC Decking | Traditional Wood Decking | Data Source |
---|---|---|---|
Embodied Energy (MJ/m³) | Moderate to High (8,000-12,000) | Low to Moderate (3,000-7,000) | [35] |
Carbon Footprint (kg CO₂e/m³) | Moderate (500-900) | Low (300-500) if sustainably sourced; High (800+) if from deforestation | [36] |
Water Usage (L/m³) | Moderate (2,000-5,000) primarily in plastic production | Moderate (2,500-6,000) primarily in tree growth and processing | [37] |
Waste Generation (kg/m³) | Low (utilizes recycled materials) | Moderate to High from harvesting and processing | [38] |
Recycled Content (% by weight) | Typically 30-70% | 0% | [39] |
Lifespan (Years) | 25-50 (premium products) | 10-30 (untreated) to 20-50+ (treated) | [40] |
Maintenance Requirements | Low (minimal cleaning) | High (regular staining, sealing, treatment) | [41] |
Potential for Recycling (%) | Moderate (infrastructure developing) | High (as raw wood or wood chips) | [42] |
Analysis: The data highlights several key environmental differences between WPC and traditional wood decking. WPC demonstrates clear advantages in recycled content utilization, directly incorporating waste materials. It also typically requires significantly less maintenance compared to traditional wood, reducing potentially harmful chemical treatment needs. WPC often boasts longer lifespan, contributing to resource efficiency over time.
However, WPC’s embodied energy can be moderate to high due to energy-intensive manufacturing processes, and its carbon footprint varies depending on production energy sources and plastic types. Traditional wood, if sourced sustainably, can have a lower initial carbon footprint, but its environmental impact increases significantly with frequent replacement or chemical treatments. While traditional wood is readily recyclable, WPC recycling infrastructure remains developing. This comparative data suggests that choosing between WPC and traditional wood decking involves trade-offs across environmental indicators, with optimal choice depending on specific priorities and circumstances.
6. Conclusion
The analysis presented indicates that wood-plastic composite (WPC) decking offers several notable environmental advantages, primarily through recycled material utilization, which helps divert waste from landfills and reduce virgin resource demand. The use of wood waste in WPC production contributes to forest conservation by decreasing virgin timber harvesting needs. Lower maintenance requirements and extended lifespan also enhance WPC decking’s environmental profile by reducing chemical treatment needs and replacement frequency.
However, important environmental considerations associated with WPC decking must be acknowledged. The manufacturing process can be energy-intensive, while reliance on virgin plastics and various additives carries environmental implications. Additionally, limitations in widespread, efficient WPC recycling infrastructure challenge end-of-life management.
In conclusion, while WPC decking presents significant environmental benefits compared to traditional wood in certain aspects, comprehensive assessment requires nuanced understanding of its entire lifecycle. The specific composition, manufacturing energy sources, and availability of effective end-of-life recycling options critically influence overall environmental friendliness. Further research and development to optimize manufacturing processes for lower energy consumption and enhance WPC recycling technologies will be crucial for maximizing this alternative decking material’s environmental benefits.
Ultimately, choosing between WPC and traditional wood decking should involve careful consideration of specific environmental goals and priorities, alongside thorough understanding of each material’s lifecycle impacts.
7. References
[1] Oklahoma State University Extension. (2020). What is Wood Plastic Composite? Retrieved from https://extension.okstate.edu/fact-sheets/what-is-wood-plastic-composite.html
[2] Cardinal Home Center. (2022). The Difference Between Wood Plastic Composite (WPC) and PVC Decking. Retrieved from https://cardinalhomecenter.com/the-difference-between-wood-plastic-composite-wpc-and-pvc-decking/
[3] General Kinematics. (2024, June 7). Wood Plastic Composite Uses & Benefits. Retrieved from https://www.generalkinematics.com/blog/wood-plastic-composite-uses-benefits/
[4] Ecoscape UK. (2023). What is Wood Plastic Composite (WPC) Decking Made Of? Retrieved from https://ecoscape.co.uk/advice/what-is-wood-plastic-composite-wpc-decking-made-of/
[5] NeoTimber. (2022). WPC Decking. Retrieved from https://neotimber.com/decking/wpc-decking/
[6] Hosung Deck. (2021). 10 Aspects of Wood Plastic Composite Material. Retrieved from https://www.hosungdeck.com/wpc-industry-trends/10-aspects-of-wood-plastic-composite-material/
[7] Trex Company, Inc. (2023). Sustainability Report: Recycled Materials Usage. Retrieved from https://www.trex.com/our-company/sustainability/
[8] The Composite Company South Africa. (2021, September 28). A Complete Guide to WPC (Wood Plastic Composite) Composite Lumber. Retrieved from https://www.thecompositecompany.co.za/blogs/decking/a-complete-guide-to-wpc-wood-plastic-composite-composite-lumber
[9] University of Tennessee Institute of Agriculture. (2023, October). Wood-Plastic Composites. Retrieved from https://utia.tennessee.edu/publications/wp-content/uploads/sites/269/2023/10/PB1779.pdf
[10] Assured Composite. (2022). A Brief History of WPC. Retrieved from https://www.assuredcomposite.com/blog/company-news/a-brief-history-of-wpc/
[11] Thompson, D. W., Hansen, E. N., Knowles, C., & Muszynski, L. (2010). Opportunities for wood plastic composite products in the U.S. highway construction sector. BioResources, 5(3), 1336-1352.
[12] Carus, M., Eder, A., & Beckmann, J. (2014). Wood-Plastic Composites (WPC) and Natural Fibre Composites (NFC): European and Global Markets 2012 and Future Trends. Nova-Institut GmbH.
[13] Gardner, D. J., Han, Y., & Wang, L. (2015). Wood–Plastic Composite Technology. Current Forestry Reports, 1(3), 139-150.
[14] Stark, N. M., & Rowlands, R. E. (2003). Effects of wood fiber characteristics on mechanical properties of wood/polypropylene composites. Wood and Fiber Science, 35(2), 167-174.
[15] Clemons, C. (2002). Wood-plastic composites in the United States: The interfacing of two industries. Forest Products Journal, 52(6), 10-18.
[16] Butylina, S., Hyvärinen, M., & Kärki, T. (2012). A study of surface changes of wood-polypropylene composites as the result of exterior weathering. Polymer Degradation and Stability, 97(3), 337-345.
[17] TimberTech. (2023). Environmental Product Declaration: TimberTech AZEK Decking. Retrieved from https://www.timbertech.com/sustainability/
[18] Kim, J. K., & Pal, K. (2011). Recent advances in the processing of wood-plastic composites (Vol. 32). Springer Science & Business Media.
[19] Ashori, A. (2008). Wood–plastic composites as promising green-composites for automotive industries! Bioresource Technology, 99(11), 4661-4667.
[20] Najafi, S. K. (2013). Use of recycled plastics in wood plastic composites – A review. Waste Management, 33(9), 1898-1905.
[21] Kazemi Najafi, S. (2013). Use of recycled plastics in wood plastic composites – A review. Waste Management, 33(9), 1898-1905.
[22] Myrin, E. S., & Petersson, P. (2015). Life Cycle Assessment of Wood-Plastic Composites: Environmental Impact and Improvement Potentials. KTH Royal Institute of Technology.
[23] AZEK Company. (2021). Environmental, Social and Governance Report. Retrieved from https://azekco.com/sustainability/
[24] Sommerhuber, P. F., Welling, J., & Krause, A. (2015). Substitution potentials of recycled HDPE and wood particles from post-consumer packaging waste in Wood–Plastic Composites. Waste Management, 46, 76-85.
[25] Klyosov, A. A. (2007). Wood-plastic composites. John Wiley & Sons.
[26] Fabiyi, J. S., & McDonald, A. G. (2010). Effect of wood species on property and weathering performance of wood plastic composites. Composites Part A: Applied Science and Manufacturing, 41(10), 1434-1440.
[27] Teuber, L., Militz, H., & Krause, A. (2016). Processing of wood plastic composites: The influence of feeding method and polymer melt flow rate on particle degradation. Journal of Applied Polymer Science, 133(13).
[28] Morrell, J. J., Stark, N. M., Pendleton, D. E., & McDonald, A. G. (2010). Durability of wood-plastic composites. In 10th International Conference on Wood & Biofiber Plastic Composites (pp. 71-76).
[29] Jawaid, M., & Khalil, H. A. (2011). Cellulosic/synthetic fibre reinforced polymer hybrid composites: A review. Carbohydrate polymers, 86(1), 1-18.
[30] Bergman, R., Falk, R. H., Salazar, J., Gu, H., Napier, T., & Meil, J. (2013). Life-cycle energy and GHG emissions for new and recovered softwood framing lumber and hardwood flooring considering end-of-life scenarios (Research Paper FPL-RP-672). U.S. Department of Agriculture, Forest Service, Forest Products Laboratory.
[31] Sommerhuber, P. F., Wang, T., & Krause, A. (2016). Wood–plastic composites as potential applications of recycled plastics of electronic waste and recycled particleboard. Journal of Cleaner Production, 121, 176-185.
[32] Bolin, C. A., & Smith, S. (2011). Life cycle assessment of ACQ-treated lumber with comparison to wood plastic composite decking. Journal of Cleaner Production, 19(6-7), 620-629.
[33] La Mantia, F. P., & Morreale, M. (2011). Green composites: A brief review. Composites Part A: Applied Science and Manufacturing, 42(6), 579-588.
[34] Bledzki, A. K., & Faruk, O. (2004). Wood fiber reinforced polypropylene composites: Compression and injection molding process. Polymer-Plastics Technology and Engineering, 43(3), 871-888.
[35] Bolin, C. A., & Smith, S. T. (2011). Life cycle assessment of borate-treated lumber with comparison to galvanized steel framing. Journal of Cleaner Production, 19(6-7), 630-639.
[36] Bergman, R., & Bowe, S. A. (2008). Environmental impact of producing hardwood lumber using life-cycle inventory. Wood and Fiber Science, 40(3), 448-458.
[37] Khalid, M. Y., Arif, Z. U., Ahmed, W., & Arshad, H. (2021). Mechanical and thermal properties of wood-plastic composites: A review. Iranian Polymer Journal, 30, 467-489.
[38] Schwarzkopf, M. J., & Burnard, M. D. (2016). Wood-plastic composites—Performance and environmental impacts. In Environmental Impacts of Traditional and Innovative Forest-based Bioproducts (pp. 19-43). Springer, Singapore.
[39] Adhikary, K. B., Pang, S., & Staiger, M. P. (2008). Dimensional stability and mechanical behaviour of wood–plastic composites based on recycled and virgin high-density polyethylene (HDPE). Composites Part B: Engineering, 39(5), 807-815.
[40] Youngquist, J. A., Myers, G. E., Muehl, J. H., Krzysik, A. M., & Clemons, C. M. (1995). Composites from recycled wood and plastics. USDA Forest Service, Forest Products Laboratory.
[41] Clemons, C. M., & Ibach, R. E. (2004). Effects of processing method and moisture history on laboratory fungal resistance of wood-HDPE composites. Forest Products Journal, 54(4), 50-57.
[42] Winandy, J. E., Stark, N. M., & Clemons, C. M. (2004). Considerations in recycling of wood-plastic composites. 5th Global Wood and Natural Fibre Composites Symposium, Kassel, Germany.