Blog
Wood-Plastic Composite Production: Distinctions Between Dry and Humid Climates
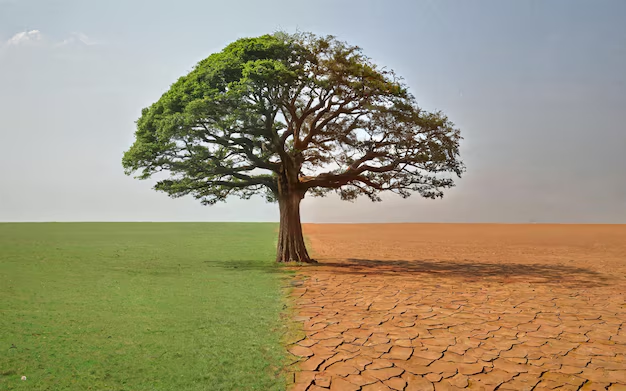
Wood-Plastic Composite Production: Distinctions Between Dry and Humid Climates
1. Introduction: The Growing Popularity of WPC and the Importance of Climate Considerations in Manufacturing
Wood-Plastic Composites (WPCs) have experienced a surge in popularity across a diverse range of applications, including construction, automotive components, and furniture. This increased adoption can be attributed to their inherent advantages such as durability, resistance to moisture, and sustainable nature. Compared to traditional wood, WPCs generally offer superior resistance to rot, decay, and pest infestations, making them a compelling alternative in various environments. While WPCs are engineered for enhanced resilience, the ambient climate in which they are produced and ultimately used plays a significant role in both the manufacturing process and the long-term performance of the final products. This report aims to delineate the key differences in establishing and operating a WPC production line in environments characterized by dry versus humid climates. By focusing on the specific challenges presented by each type of climate and the necessary adaptations required, this analysis provides valuable insights for stakeholders involved in or considering WPC manufacturing.
2. Understanding the Fundamentals of WPC Production
The production of Wood-Plastic Composites typically involves a multi-stage process. Initially, raw materials such as wood flour (derived from wood waste or other cellulose sources) and plastic resins (commonly polyethylene, polypropylene, or polyvinyl chloride) are prepared. The wood flour is often dried to a specific moisture content to ensure proper bonding with the plastic matrix. Subsequently, these materials are combined in a mixing and compounding stage, where additives like UV stabilizers, lubricants, pigments, and flame retardants are incorporated under controlled heat. The resulting molten composite is then formed into the desired profiles or shapes through processes such as extrusion, injection molding, or compression molding. Finally, the formed product undergoes cooling and finishing processes, which may include sanding, embossing, or the application of a co-extruded protective layer to enhance its properties. The typical composition of WPC involves a significant proportion of wood flour, ranging from 50% to 70% by weight, combined with 30% to 50% plastic and up to 10% additives. It is important to note that the specific manufacturing process and material formulation can be tailored to meet the requirements of the intended application of the final WPC product, allowing for a wide range of properties and characteristics.
3. WPC Production in Dry Climates: Challenges and Solutions
- 3.1 Lower Moisture Content in Raw Materials: Implications and Necessary Adjustments in Drying Processes In dry climates, the ambient air typically holds less moisture, which can result in a lower initial moisture content in the wood flour used for WPC production. Air with low humidity can cause wood to release water molecules, leading to a drier raw material. While a lower moisture content might initially seem advantageous by reducing the need for extensive drying, it is crucial to recognize that excessively dry wood flour can potentially hinder the proper bonding between the wood fibers and the polymer matrix during the compounding stage. For optimal composite performance, organic fillers like wood flour need to be dried appropriately to facilitate a strong and uniform bond with the plastic. Even in dry climates, achieving the target moisture content, which typically ranges from 2% to 8% depending on the specific manufacturing platform and plastic type, may still necessitate controlled drying processes. Consistent monitoring of the wood flour’s moisture content is essential, as both excessively high and excessively low levels can lead to issues such as void formation within the composite structure and compromised mechanical properties in the final product. Furthermore, while the effect is generally less pronounced than on wood flour, some plastic resins can also be affected by very low humidity, potentially leading to an increase in brittleness. However, research suggests that under warm and dry conditions, some materials might even exhibit a slight increase in mechanical properties, indicating that the impact of very low humidity on plastics can be complex and material-dependent.
- 3.2 Increased Risk of Static Electricity: Impact on Production and Mitigation Strategies The dry air prevalent in dry climates exhibits lower electrical conductivity, which significantly increases the potential for static electricity buildup during the handling of dry wood flour and plastic pellets in a WPC production facility. Maintaining a relative humidity level between 40% and 60% has been shown to drastically reduce static electricity in plastic production environments, highlighting the impact of moisture on charge dissipation. The accumulation of static charge can lead to various operational challenges, including the sticking of dry materials to processing equipment, which can disrupt the smooth flow of production. Additionally, static can cause uneven mixing of the wood flour and plastic pellets, potentially affecting the uniformity and overall quality of the final WPC product. In the case of fine wood dust, a significant buildup of static electricity can even pose a fire hazard. To mitigate these risks in dry climates, several strategies can be implemented. Maintaining a slightly higher humidity level within the production facility through the use of humidification systems, aiming for the 40-60% relative humidity range typically recommended for plastics processing, is an effective approach. While not explicitly mentioned in the provided snippets, the use of anti-static additives in the WPC formulation can also help to reduce charge buildup within the material itself. Furthermore, implementing grounding and bonding techniques for all processing equipment can provide pathways for static charges to safely dissipate, minimizing the risks of material handling issues and potential hazards.
- 3.3 Potential for Faster Cooling and Solidification: Effects on Product Quality and Process Optimization The lower humidity characteristic of dry climates can lead to faster rates of evaporation, which in turn can potentially result in quicker cooling and solidification of the WPC product after it has been extruded or molded. In composite manufacturing, the level of humidity can influence the efficiency and effectiveness of drying and curing times, suggesting that drier air can accelerate these processes. While faster cooling might seem like an advantage in terms of increasing production speed and throughput, it is important to consider that uncontrolled or excessively rapid cooling can potentially induce internal stresses within the WPC material or lead to warping of the final product. Research indicates that if the cooling process occurs too quickly, the material’s temperature might drop below the optimal forming range prematurely, which can negatively impact the overall quality of the product. Therefore, in dry climates, careful control over the cooling rates is necessary to ensure the integrity and desired properties of the WPC product. This might involve adjusting cooling times, utilizing cooling systems with regulated temperatures, or implementing post-cooling treatments to manage any potential internal stresses that may have developed due to rapid solidification.
4. WPC Production in Humid Climates: Challenges and Solutions
- 4.1 Higher Moisture Content in Raw Materials: Impact on Storage, Handling, and Drying Requirements Humid climates are characterized by a high concentration of moisture in the air, which significantly impacts the raw materials used in WPC production, particularly wood flour. Wood is a hygroscopic material, readily absorbing and releasing moisture to reach equilibrium with the surrounding air. In humid conditions, this leads to a higher initial moisture content in wood flour, creating an environment conducive to mold growth, fungal decay, and clumping of the material. Prolonged exposure to moisture can allow fungal attacks to occur within the wood component of WPCs. To mitigate these issues, proper storage of wood flour is crucial. Storing the material in sealed containers or climate-controlled environments helps to prevent excessive moisture absorption from the humid air. Ideally, storage areas should be kept as dry as possible, and WPC products should be placed on flat surfaces to avoid warping. In some cases, using a dry lumber cover or tarp can provide additional protection. Given the higher initial moisture content in humid climates, more extensive and energy-intensive drying processes are typically required to reduce the moisture content of the wood flour to the acceptable range of 2% to 8%. Various drying methods, such as steam tubes and rotary drum dryers, are employed to remove moisture before the wood flour is compounded with the plastic. Even plastic pellets, which are generally more resistant to moisture absorption than wood flour, can still accumulate surface moisture in humid environments, potentially necessitating pre-drying to ensure proper melt flow during processing and prevent defects in the final product.
- 4.2 Risk of Moisture Absorption and Swelling: Effects on Product Quality and Dimensional Stability Even after the WPC production process is complete, products manufactured in or intended for use in humid climates face a higher risk of absorbing ambient moisture. The wood component within the composite material is primarily responsible for this moisture sorption. Prolonged exposure to high humidity can lead to swelling and warping of the WPC product, which can negatively impact its dimensional stability and potentially reduce its mechanical strength over time. For instance, WPC deck boards have been shown to experience a significant loss of bending modulus of elasticity due to water absorption. To combat these issues, the incorporation of additives such as fungicides and mildewcides becomes particularly important in WPC formulations designed for humid environments, helping to inhibit biological degradation. While the polymer matrix in WPCs does offer a degree of protection to the wood fibers by encapsulation, the overall effectiveness of this barrier can vary depending on the quality of the composite and the specific processing methods employed. It is also crucial to consider the intended end application of the WPC product. For example, WPC intended for outdoor decking in humid regions will require a higher degree of moisture resistance compared to products used indoors in drier environments.
- 4.3 Increased Potential for Mold and Fungal Growth: Implications for Raw Materials and Finished Products The high levels of moisture present in humid climates create an ideal environment for the proliferation of mold and fungi. This poses a significant concern for both the stored raw materials, especially wood flour, and the finished WPC products. Mold and fungal growth can negatively affect the aesthetic appearance of the materials and, in some cases, compromise their structural integrity. For wood flour stored in humid conditions, the risk of fungal contamination is particularly high, potentially rendering it unusable for production. Similarly, finished WPC products exposed to prolonged high humidity can develop surface mold, which can be difficult to remove and may lead to further degradation of the material. To mitigate this risk, ensuring proper ventilation in both storage areas and during the production process is essential. Additionally, incorporating anti-mold and anti-fungal additives into the WPC formulation is a critical step for products intended for use in humid environments. Surface treatments or coatings can also be applied to the finished WPC products to provide an extra layer of protection against moisture penetration and subsequent microbial growth.
- 4.4 Corrosion Concerns for Equipment: Preventive Measures and Material Selection High humidity levels in the atmosphere can significantly accelerate the rate of corrosion in metal components found in WPC production equipment. This is particularly relevant for critical machinery such as molds, extruders, and cooling systems, which often come into direct contact with moisture or are exposed to the humid ambient air. Condensation, which readily forms on surfaces in high-humidity environments, can lead to the development of rust and potential malfunctions in sensitive equipment. To address these concerns, a range of preventive measures can be implemented. Maintaining a controlled humidity level within the production facility through the use of dehumidification systems is a primary strategy. Selecting corrosion-resistant materials, such as stainless steel or specialized alloys, for the construction of critical equipment components can also significantly enhance their longevity in humid conditions. Implementing regular cleaning and maintenance schedules is crucial, including the routine application of rust inhibitors and protective coatings on exposed metal surfaces, especially during periods when the equipment is not in active use. Ensuring proper ventilation throughout the facility can help to minimize the buildup of humidity and reduce the formation of condensation. In areas housing particularly sensitive equipment, the use of dedicated dehumidifiers might be necessary to maintain optimal conditions and prevent corrosion-related issues.
5. Raw Material Management: A Climate-Sensitive Approach
- 5.1 Storage Best Practices for Wood Flour in Dry vs. Humid Environments In dry climates, the primary focus for storing wood flour should be on preventing it from becoming excessively dry, as this can potentially affect its ability to bond effectively with the plastic matrix during the WPC manufacturing process. Storing wood flour in covered areas, such as warehouses or sheds, can help to shield it from direct sunlight and wind, which can contribute to excessive drying. Depending on the specific requirements of the production process, maintaining a minimal level of humidity control within the storage facility might be beneficial to prevent the wood flour from losing too much moisture. Conversely, in humid climates, the priority shifts to preventing the wood flour from absorbing excessive moisture from the air, which can lead to mold growth, fungal decay, and clumping. To achieve this, wood flour should ideally be stored in airtight containers or silos that are elevated off the ground to minimize contact with ground moisture. Storage areas should be well-ventilated to encourage air circulation and reduce humidity levels. In regions with very high humidity, utilizing climate-controlled warehouses equipped with dehumidification systems can provide an optimal storage environment. Implementing moisture barriers, such as polyethylene sheeting, in the storage area can also help to prevent moisture migration and protect the wood flour. Regardless of the climate, regular inspection of the stored wood flour is essential. In humid conditions, particular attention should be paid to identifying any signs of mold growth or clumping, which could indicate excessive moisture absorption.
- 5.2 Storage Best Practices for Plastic Pellets in Dry vs. Humid Environments The storage of plastic pellets in dry climates is generally less critical compared to wood flour, as most common plastics used in WPC production are not as hygroscopic. However, it is still advisable to store plastic pellets in covered hoppers or containers to protect them from dust and other contaminants. In extremely dry conditions, there is a potential for increased static electricity buildup, so measures to mitigate static might be considered in the storage area as well. In humid climates, the primary concern for storing plastic pellets is to protect them from absorbing surface moisture, which can potentially affect their flowability and processing characteristics during extrusion or molding. Storing pellets in sealed containers or silos is recommended to minimize exposure to humid air. In areas with very high humidity, utilizing storage facilities with dehumidification systems can provide an extra layer of protection. For certain types of plastics that are more hygroscopic, such as nylon and ABS, more stringent humidity control during storage might be necessary. Regardless of the climate, it is important to prevent contamination of plastic pellets from dust and airborne particles. In dry climates, static electricity can exacerbate dust attraction, while in humid climates, moisture can cause dust to adhere to the pellets, potentially leading to surface defects in the final WPC product.
- 5.3 Optimizing Drying Processes for Wood Flour Based on Climate In dry climates, where the initial moisture content of wood flour is likely to be lower, the drying process might require less energy and a shorter duration to reach the target moisture content of 2% to 8%. The focus should be on carefully monitoring the outlet air temperature and moisture levels of the drying equipment to ensure that the wood flour is dried sufficiently without becoming excessively dry, which could negatively impact bonding with the plastic. Energy-efficient drying technologies should still be considered to minimize operational costs. In humid climates, the drying process for wood flour will typically be more energy-intensive due to the higher initial moisture content. Utilizing efficient drying methods, such as steam tube dryers or rotary drum dryers, is crucial for effectively removing the excess moisture. For wood flour with very high moisture content, implementing a two-stage drying process might be beneficial, where the material undergoes an initial bulk drying phase followed by a more controlled final drying stage. The aim is to consistently achieve a low moisture content within the 2% to 8% range to prevent processing issues like foaming or voids, and to ensure the production of high-quality WPC with optimal mechanical properties. It is important to recognize the direct link between proper drying of wood flour and the prevention of issues such as gas pressure buildup during high-temperature processing, which can lead to voids and ultimately compromise the mechanical integrity of the final WPC product.
6. Adapting the Production Process to Environmental Conditions
- 6.1 Temperature and Humidity Control within the Manufacturing Facility: Importance and Implementation in Dry and Humid Climates Maintaining a stable and controlled temperature and humidity level within the WPC manufacturing facility is of paramount importance for ensuring consistent product quality, particularly given the sensitivity of the raw materials and the production process to fluctuations in these environmental conditions. In dry climates, the primary focus of climate control is often on preventing excessive dryness and the associated buildup of static electricity. To achieve this, the implementation of humidification systems might be necessary to maintain a relative humidity level within the range of 40% to 60%, which is generally recommended for plastics processing to minimize static discharge. Additionally, precise temperature control is crucial throughout the WPC manufacturing process, from the storage of raw materials to the compounding and forming stages, to prevent the thermal degradation of the wood flour and ensure the proper processing of the plastic resins. In contrast, WPC production facilities located in humid climates face the challenge of controlling high moisture levels in the air. In these environments, dehumidification becomes essential to prevent issues such as condensation on equipment surfaces, the growth of mold and mildew within the facility, and the accelerated corrosion of metal machinery. Robust HVAC (Heating, Ventilation, and Air Conditioning) systems with dehumidification capabilities are typically required to maintain low humidity levels and a stable temperature. While dehumidification is the primary concern, temperature control remains equally vital for the proper processing of the WPC materials. It is important to note that the selection and operation of HVAC systems can have significant energy consumption and cost implications, particularly with the anticipated rise in HVAC equipment prices due to evolving environmental regulations. Therefore, optimizing building design and insulation to minimize the load on HVAC systems is a crucial consideration in both dry and humid climates.
- 6.2 Extrusion and Molding Considerations: Adjusting Parameters for Optimal Results in Different Climates While the fundamental principles of extrusion and molding remain consistent across different climates, subtle adjustments to processing parameters might be necessary to achieve optimal results in dry versus humid environments. In dry climates, the lower ambient humidity could potentially lead to a slightly faster cooling rate of the molten WPC material during extrusion or molding. This might necessitate adjustments to cycle times or the temperature of cooling systems to prevent issues like warping and ensure proper solidification of the product. Furthermore, the typically lower moisture content of the wood flour in dry climates could influence the melt viscosity of the composite, potentially requiring minor modifications to processing temperatures or the rotational speed of the extruder screws to maintain consistent flow and mixing. In humid climates, even with thorough drying, the wood flour might still retain a slightly higher residual moisture content compared to that in dry climates. During the high-temperature extrusion or molding process, this residual moisture can lead to increased gas pressure within the material, potentially causing the formation of voids or surface defects in the final product. Therefore, in humid climates, ensuring that the wood flour is dried as thoroughly as possible is paramount. Maintaining optimal melt temperatures during processing is also crucial to ensure that the polymer effectively encapsulates the wood fibers, which helps to mitigate moisture absorption in the final WPC product. Regardless of the climate, precise control over the die temperature during extrusion is critical for achieving the desired surface quality and dimensional accuracy of the WPC profiles.
- 6.3 Cooling Stage Management: Strategies to Ensure Product Integrity in Varying Humidity Levels The management of the cooling stage in WPC production is crucial for setting the final properties of the product and can be influenced by the ambient humidity levels. In dry climates, where cooling might occur more rapidly due to the lower moisture content in the air, it is important to ensure that the WPC product cools uniformly to prevent the development of internal stresses that could lead to warping or cracking. Implementing controlled cooling methods, such as the use of cooling tunnels with regulated temperatures or water baths, can help to achieve this uniform cooling. In humid climates, the high moisture content in the air can potentially slow down the evaporation of any residual moisture from the surface of the WPC product, which might affect the rate of solidification. Therefore, ensuring an adequate cooling time and potentially increasing airflow around the product during cooling can be beneficial in facilitating proper solidification and preventing moisture-related defects. In both dry and humid climates, it is essential to handle the WPC products carefully during and after the cooling stage to avoid any physical damage that could compromise their structural integrity or surface finish.
7. Equipment and Facility Maintenance in Diverse Climates
- 7.1 Combating Corrosion in Humid Environments: Material Choices and Maintenance Protocols As previously discussed, the risk of corrosion in WPC production equipment is significantly elevated in humid environments. To effectively combat this, a comprehensive strategy involving both the selection of appropriate materials and the implementation of stringent maintenance protocols is necessary. For critical equipment components that are prone to corrosion, such as molds and extruder screws, choosing corrosion-resistant materials like stainless steel or specialized alloys is a fundamental step. Additionally, the application of protective coatings or surface treatments can significantly enhance a mold’s resistance to corrosion. A robust maintenance protocol should include regular and thorough cleaning of all equipment to remove dust, debris, and any contaminants that could potentially trap moisture and promote corrosion. Implementing a schedule for the routine application of rust inhibitors and protective coatings on all exposed metal surfaces, particularly during periods of equipment inactivity, is also crucial. Regular inspections of equipment should be conducted to identify any early signs of corrosion, and any issues detected should be addressed promptly to prevent further damage. Ensuring proper ventilation within the production facility is essential to minimize the buildup of humidity and reduce the formation of condensation on equipment surfaces. In areas housing particularly sensitive equipment, the use of dehumidifiers can provide an additional layer of protection by maintaining a consistently low humidity level.
- 7.2 General Equipment Upkeep: Best Practices for Ensuring Longevity in Both Dry and Humid Conditions Regardless of the ambient climate, consistent and thorough general equipment upkeep is essential for ensuring the longevity and operational efficiency of a WPC production line. This includes establishing a regular cleaning schedule for all machinery to prevent the accumulation of dust, which can be more prevalent in dry climates due to static electricity, and to remove any moisture that might accumulate in humid conditions. Adhering to the manufacturer’s guidelines for lubrication and maintenance schedules for all key equipment, including extruders, molds, and cooling systems, is crucial for preventing premature wear and tear. Periodic inspections of electrical systems should be conducted to identify any signs of damage or wear, which can be exacerbated by high humidity leading to corrosion. Furthermore, it is important to regularly calibrate temperature and pressure sensors to ensure accurate processing conditions are maintained, as precise control of these parameters is vital for producing high-quality WPC products in both dry and humid climates.
8. Quality Control and Assurance: Maintaining Standards Across Climates
- 8.1 Moisture Content Monitoring: Critical Control Points in Dry and Humid Production Monitoring the moisture content of raw materials, particularly the incoming wood flour, is a critical quality control measure in WPC production, irrespective of the climate. Ensuring that the wood flour meets the required moisture specifications (typically 2-8%) is essential for achieving proper bonding with the plastic and preventing processing issues. Regular checks of the moisture content in the final WPC product are also important to verify that it aligns with established quality standards and will perform as expected in its intended application. In humid climates, where the risk of moisture absorption is higher, more frequent and rigorous monitoring of moisture levels might be necessary at various intermediate stages of the production process to ensure that moisture is being adequately controlled and that the materials are not exceeding acceptable limits.
- 8.2 Dimensional Stability Testing: Ensuring Product Consistency Despite Environmental Variations To ensure the consistency and reliability of WPC products, conducting tests to assess their dimensional stability under varying temperature and humidity conditions is crucial. This is particularly important for WPC products that are intended for outdoor applications or for use in climates that experience significant fluctuations in temperature and humidity throughout the year. Standardized tests, such as water absorption tests and thickness swelling tests (e.g., following ASTM standards), should be performed to quantify the material’s response to moisture exposure. These tests provide valuable data on how much moisture the WPC absorbs and how much it swells as a result, which are key indicators of its long-term performance and durability in different environmental conditions.
- 8.3 Performance Testing: Evaluating WPC Products Under Simulated Dry and Humid Conditions A comprehensive quality control program for WPC products should include performance testing conducted under conditions that simulate both dry and humid climates. This often involves exposing WPC samples to controlled environments with varying temperatures and humidity levels in environmental chambers to assess their long-term performance. After exposure to these simulated conditions, the mechanical properties of the WPC, such as tensile strength, flexural strength, and impact resistance, should be evaluated to determine if they have been affected by the environmental exposure. For products intended for humid climates, assessing their resistance to mold and fungal growth is particularly important. Additionally, the color stability and resistance to UV degradation of the WPC should be evaluated, as these properties can be influenced by both temperature and humidity, especially in outdoor applications.
9. Energy Consumption and Cost Considerations
- 9.1 Energy Requirements for Climate Control: Comparing HVAC Needs in Dry and Humid Regions The energy requirements for maintaining the necessary climate conditions within a WPC production facility can differ significantly between dry and humid regions. In dry climates, while maintaining a consistent temperature can be energy-intensive, the energy consumed for humidification to prevent static buildup might be comparatively lower than the energy required for dehumidification in humid climates. In humid climates, the process of dehumidification is typically more energy-intensive. The need to operate robust HVAC systems to maintain low humidity levels within the facility to prevent moisture-related issues such as corrosion, mold growth, and processing defects will contribute substantially to the overall operational costs. It is important to consider the impact of the facility’s design and insulation on the energy efficiency of its climate control systems. A well-insulated building envelope can significantly reduce the load on HVAC equipment in both dry and humid climates. Furthermore, the anticipated increase in the cost of HVAC equipment due to new environmental regulations aimed at phasing out refrigerants with high global warming potential will likely impact both new and existing WPC production lines, making energy-efficient climate control solutions even more critical.
- 9.2 Optimizing Drying Processes for Energy Efficiency in Different Climates Optimizing the drying process for wood flour is crucial for minimizing energy consumption in WPC production, and the strategies employed should be tailored to the specific climatic conditions. In dry climates, where the initial moisture content of the wood flour is likely to be lower, the focus should be on utilizing shorter drying times and potentially lower drying temperatures to achieve the target moisture content without over-drying the material. Exploring and implementing energy-efficient drying technologies can further reduce energy costs. In humid climates, where more extensive drying is required due to higher initial moisture levels, investing in high-efficiency drying equipment is essential. Incorporating pre-drying stages to remove a significant portion of the moisture before the main drying process can help to reduce the load on the primary dryers and improve overall energy efficiency. Additionally, exploring the use of waste heat recovery systems, where heat generated by other processes within the facility is used to pre-heat the air for drying, can be a viable strategy for reducing overall energy consumption in the drying process. It is important to acknowledge the inherent trade-off between achieving thorough drying, which is particularly critical in humid climates to prevent moisture-related issues in the final product, and the associated energy costs of the drying process.
10. Installation Guidelines for WPC Products Based on Climate
The climate where the final WPC product will be installed also plays a significant role in determining the appropriate installation guidelines. In dry climates, where temperature fluctuations can be substantial, the primary concern during installation is often accommodating the expansion and contraction of the WPC material. Ensuring that proper spacing is left between individual WPC components, such as decking boards or wall panels, is crucial to allow for these movements without causing buckling or other structural issues. Maintaining natural ventilation after installation is also important.
In humid climates, while WPC is generally more resistant to moisture than traditional wood, providing proper ventilation during installation remains important, especially for applications like decking or wall cladding, to prevent the buildup of moisture underneath the material or behind panels. Acclimation of the WPC product to the temperature and humidity conditions of the installation environment for a period of 24 to 48 hours prior to installation is generally recommended in both dry and humid climates to allow the material to adjust and minimize potential issues after installation. Furthermore, the use of moisture barriers, such as 6-mil polyethylene sheeting, is often recommended, particularly when installing WPC flooring over concrete subfloors in both dry and humid environments, to prevent moisture migration from the ground that could lead to mold growth or other moisture-related problems.
11. Conclusion: Optimizing WPC Production for Specific Climatic Conditions
Establishing and operating a Wood-Plastic Composite (WPC) production line presents distinct challenges and requires tailored solutions depending on whether the facility is located in a dry or a humid climate. In dry climates, manufacturers must focus on managing potentially low initial moisture content in raw materials, mitigating the increased risk of static electricity, and carefully controlling faster cooling rates during processing. Strategies such as moisture monitoring, the use of humidification systems, and controlled cooling protocols are essential for maintaining product quality and operational efficiency.
Conversely, humid climates pose challenges related to high moisture content in raw materials, the risk of moisture absorption and swelling in finished products, increased potential for mold and fungal growth, and accelerated corrosion of equipment. Extensive drying processes, proper storage in climate-controlled environments, the incorporation of anti-microbial additives, and robust equipment maintenance protocols are crucial for successful WPC production in these regions.
Regardless of the climate, implementing climate-specific strategies for raw material management, adapting the production process to environmental conditions, ensuring diligent equipment maintenance, and maintaining stringent quality control measures are paramount. Understanding and proactively addressing the unique challenges presented by dry and humid climates is not only essential for achieving efficient and cost-effective WPC production but also for ensuring the long-term performance and durability of the final products. As the market for WPCs continues to expand globally, adopting climate-conscious manufacturing practices will become increasingly important for manufacturers seeking to remain competitive and sustainable in diverse environmental conditions.